
Nel cuore degli stabilimenti Michelin scopriamo come viene costruito uno pneumatico per auto
Gli pneumatici per auto sono tutti simili, “ciambelle nere e gommose”. Ciò che distingue uno pneumatico di qualità sono le performance di durata, sicurezza e comfort. Tutti caratteri che provengono da un attento lavoro di ricerca del miglior equilibrio di prestazioni in tutte le condizioni di utilizzo. E' in fase di produzione però che l'impegno di un Produttore diventa davvero tangibile, attraverso efficienti processi di produzione manuali o totalmente automatizzati in cui la verifica finale di ogni gomma costruita spetta però ancora all'uomo. Ecco come nascono gli pneumatici Michelin da oltre 50 anni.
L'UOMO E IL ROBOT – In occasione del 50° anniversario dello stabilimento Michelin di Cuneo, il più grande d'Europa, abbiamo visto come si producono gli pneumatici destinati alle Case costruttrici e quelli per il mercato del ricambio. Insieme ai tecnici Michelin abbiamo scoperto cosa sono e dove finiscono gli pneumatici imperfetti. La costruzione di uno pneumatico Michelin avviene unendo gomma, fili metallici, tele tessili e tele metalliche in misura variabile in base alla tipologia e alle dimensioni dello pneumatico che si vuole ottenere. Per il trasporto pesante ad esempio i tessuti tessili lasciano completamente spazio alle tele metalliche, molto più adatte ai carichi e alle sollecitazioni di un camion. Dalla preparazione dei semifiniti (profilati di gomma, tessili e metallici) al confezionamento (unione dei semifiniti) fino alla finizione e vulcanizzazione, gli impianti automatizzati dello stabilimento di Cuneo consentono di produrre 14 milioni di pneumatici all'anno. Vi chiederete dov'è il valore aggiunto dell'uomo, fattore chiave del successo Michelin nel mondo? Lo troviamo soprattuto nell'esperienza dei tecnici Michelin impegnati a controllare la perfezione di ogni pneumatico che sfornano le presse di cottura. Ma vediamo passo per passo come nasce uno pneumatico.
LE SCARPE AUTO SU MISURA – Nel reparto di produzione per auto e trasporto leggero abbiamo visto in azione le linee automatiche (per Energy Saver e Alpin) e le linee individuali d'alta gamma; quegli pneumatici (come Pilot Sport 3 e Pilot Super Sport) che il Produttore francese progetta su misura per le auto più performanti delle Case costruttrici più prestigiose. Tra le due tipologie la differenza sostanziale sta nella fase di confezione e finizione, che avvengono in step consecutivi sulle linee automatiche o in parallelo su quelle individuali in un tempo dai 12 ai 40 centesimi di minuto. Tutto inizia dalla costruzione della parte interna dello pneumatico, la carcassa, costruita su un tamburo rotante. Sullo strato interno di gomma impermeabile, che garantisce tenuta allo pneumatico gonfiato (come la vecchia camera d'aria), vengono applicati i cerchietti metallici laterali che terranno la gomma solidale al cerchio. Le macchine MAC6 (Macchine Automatiche di Confezionamento), installate nel 2010, applicano il pacco di cintura formato da tele tessili di rayon e nylon e tele metalliche. I fili metallici che compongono le tele radiali e i cerchietti vengono prodotti negli stabilimenti Michelin di Fossano, dove da una vergella (una barra di acciaio semilavorato avvolta in matasse) di oltre un centimetro si ricavano i fili di diametro inferiore al millimetro che giungono allo stabilimento di Cuneo. Segue l'applicazione di alcuni elementi di rinforzo (strisce di gomma) per rendere più resistenti le zone del tallone e della spalla dello pneumatico.
QUASI UNA GOMMA – A questo punto il tamburo flessibile, gonfiandosi al centro, dà allo pneumatico per la prima volta una forma molto simile a quella definitiva, ma è ancora presto perché sia sicuro e flessibile. Ai due lati della gomma vengono, infatti, applicati i fianchi esterni. La loro rigidità è fondamentale per evitare che lo pneumatico si stalloni dal cerchio per le deformazioni laterali senza però compromettere il comfort e la guidabilità dell'auto. Il confezionamento termina con l'applicazione e la finizione del battistrada. Riscaldando semplicemente il nastro di gomma morbida a 70 °C si sovrappongono le due estremità del battistrada tagliate in obliquo affinché creino continuità senza provocare rigonfiamenti nel punto di saldatura.
COSA SONO I BOLLINI COLORATI? – Avete mai notato che sul fianco dei vostri nuovi pneumatici ci sono dei bollini colorati di rosso, bianco o verde? E' in quel punto che il battistrada ha un maggior “accumulo di peso” il bollino è un'indicazione utile per chi durante l'installazione effettua il montaggio e l'equilibratura della gomma sul cerchio con i pesi. Ora lo pneumatico si può considerare costruito ma la gomma è talmente soffice e malleabile al tatto che non durerebbe più di qualche metro. Tecnicamente, infatti, a questo stadio la gomma si definisce “cruda” poiché non ha ancora acquisito le caratteristiche fisco-chimiche della vulcanizzazione. Intanto un piccolo codice a barre sul tallone segue dall'origine del processo ogni pneumatico e ne identifica tutti i componenti e i semifiniti utilizzati. Dopo un controllo visivo di collaggi e saldature da parte di un operatore ogni pneumatico passa al reparto di stampaggio e cottura.
COTTA E INTAGLIATA IN 13 MINUTI – L'ultima fase della produzione di uno pneumatico Michelin avviene in una delle 450 presse, dove si svolge anche quella più lunga. Lo stampo in cui lo pneumatico riceve la tassellatura del battistrada, le informazioni sui fianchi e la cottura è diviso in due conchiglie simmetriche. La campana superiore si alza e accoglie dall'alto la gomma cruda in cui entra una membrana di compressione. Quando la campana superiore si abbassa comprime i settori dello stampo dall'esterno mentre dall'interno la membrana si riempie di acqua calda e comprime contemporaneamente la carcassa dall'interno. Durante la vulcanizzazione, che avviene con particolari cicli fino a 160 °C e 16 bar, per un tempo variabile da 9 a 13 minuti in base alle dimensioni dello pneumatico, lo zolfo contenuto nella mescola si lega alle catene polimeriche per cui la gomma passa da uno stato plastico a uno elastico. La vita di uno stampo è davvero dura e breve, basta pensare che dopo l'equivalente di una produzione giornaliera la mescola aggredisce la ghisa al punto da renderlo inutilizzabile. Gli stampi delle gomme invernali Alpin durano ancora meno di 50 mila cicli, per la particolare tipologia di mescola e forma delle lamelle da imprimere nel battistrada. Dopo non resta altro che verificare la qualità ma non prima aver fatta raffreddare le gomme sugli appositi tappeti di trasferimento.
IL CONTROLLO E' MANUALE – Chi l'avrebbe mai detto che tutti gli oltre 40.000 pneumatici Michelin prodotti in media ogni giorno vengono controllati uno ad uno? Eppure la fase finale consiste proprio nella ricerca di eventuali imperfezioni (in 40 centesimi di minuto) e classifica del difetto (in 1 minuto). Un lavoro che solo gli occhi esperti di tecnici adeguatamente specializzati possono fare. Se una gomma presenta lievi danni estetici passa al settore di sbarbatura, dove viene asportato un sottile strato di gomma nell'orine di qualche decimo di millimetro. Diversamente, se il danno è strutturale o tale da inficiarne le performance, le gomme vengono tagliate sui fianchi per azzerare il rischio che anche per errore passino al magazzino. Un controllo finale, a campione, con la macchina CID ne simula il montaggio sul cerchio e la percorrenza di un percorso di prova.
PRIMA E SECONDA SCELTA? – Spesso, tra gli appassionati e gli automobilisti comuni, si sente parlare di pneumatici di seconda scelta; in realtà, secondo quanto appreso dai tecnici Michelin, non esistono pneumatici di qualità inferiore ma solo pneumatici che non rispettano gli standard identificativi richiesti dai Costruttori auto. Di cosa stiamo parlando? Delle tracciature colorate che vedete ogni volta sul battistrada delle gomme nuove. Quelle righe rappresentano per i Costruttori auto delle informazioni ben precise utili sulle linee di assemblaggio. Se una di queste righe dovesse mancare, la gomma viene “declassificata” da Original Equipment a Replacement e destinata ai gommisti come ricambio, qualitativamente identico agli stessi pneumatici montati sulle auto nuove.
MAGAZZINO AUTOMATICO – Lo stoccaggio del prodotto finito è affidato ai robot Kuka, che palettizzano automaticamente le gomme in base alla dimensione prelevandole da un nastro. A pochi metri di distanza si svolge curiosamente l'apposizione manuale dell'etichetta europea su ogni pneumatico, un lavoro dove l'uomo è ancora più efficiente di qualsiasi altra macchina sperimentata nello stabilimento di Cuneo. Dopo circa 15 minuti effettivi di lavorazione (esclusi i tempi di trasferimento e riposo) gli pneumatici Michelin finiscono nel deposito di stoccaggio, dove in circa 10 giorni avviene il ricambio complessivo dei 400 mila pneumatici, in attesa di essere distribuiti e pronti per essere installati su qualsiasi auto circolante in Europa (il 93% della produzione finisce all'estero).
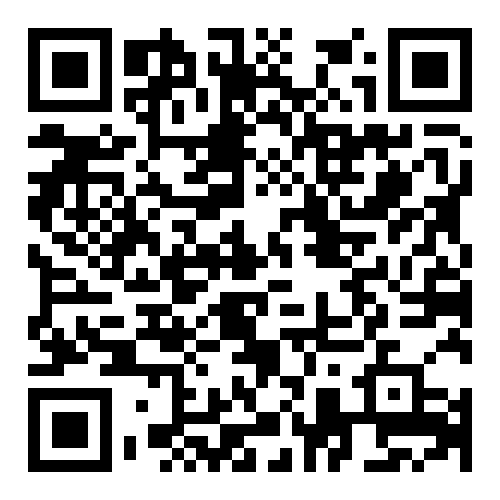
Iscriviti gratis al nostro canale whatsapp cliccando qui o inquadrando il QR Code